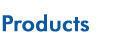
Press Felts For Paper Industry
Forming Fabric
The forming fabric or wire of a paper machine is the continuous belt or belts of mesh screen upon which the paper sheet is formed. Most modern forming fabrics are no longer comprised of metal wires. Rather, they are comprised of monofilament polyester strands. The weave pattern and layering of a forming fabric is designed to meet stringent requirements of dimensional stability, resistance to abrasion (on the wire side), minimum resistance to drainage, minimum wire-mark, and (sometimes) maximization of retention of fiber fines
General specification of forming fabrics
- Single layer 3 shaft fabric is suitable for making pulp and packing papers
- Single layer 4 shaft fabric is suitable for making culture, printing and packing papers etc
- Single layer 5 shaft fabric is suitable for making toilet paper, printing and packing papers etc
- Double layer 7 shaft;fabric is suitable for quality printing paper and tissue paper etc
- Single layer 8 shaft fabric is suitable for making high basic weight paper and packing papers
- Two and half layer 16 shaft fabric is suitable for making quality printing paper, tissue paper and surface pulp, inner pulp and base pulp
- Three layer multi-shaft fabric is suitable for making quality printing paper, tissue paper and cigarette paper etc
Dryer Fabric
The material which we use is a variety of monofil made from Thermax polymer. This provides superior hydrolytic stability, longer degradation periods and high residual strength, giving longer life to the fabrics during use
We produces the complete sort of standard drying fabrics for the production of all paper types
- According to the weaving, it can be divided into three or four shed
- According to the weaving, it can be divided into three or four shed
- According to the types it can be divided into one and half layer or double layers
- According to joining, it can be divided into seamless, spiral ring and pin joining
- 3-shed one layer and a half fabric is suitable for drying papers below 70g
- According to the weaving, it can be divided into three or four shed
- 4-shed double layer fabric is suitable for drying papers above 70g
Press Felt The Structures of Paper making Felt
There are three series of paper making felts available in the market. Namely, they are single layer mesh, double layer mesh and complex mesh. Depending on their structures, thet can be divided into formed felt, pressed felt, upper felt, dried felt, pulp board felt and so on.
Paper making felts are generally made of the base mesh layer and the fiber layer. The base mesh can be single,double or complex. All mesh bases are woven by monofilament or twisted monofilament yarns. The fiber layers are woven by different sizes of polyamide fibers. Fiber layer and base mesh layer are attached by needle stitching to form the felt. The Functions and Performance of Paper making Felt
Paper making Felt has the following functions and performance
- Super water filtration and air ventilation; larger gap makes cleaning a lot easier and less likely to get jammed. Best result for dewatering of grain mark press, vacuum press, blind hole press
- Excellent elasticity and uncompressible. High tolerance for linear pressure, especially on complex pressed felt. It can handle up to 200KN/M of linear pressure.Efficiently lower the volume of pressed water from the paper, thus lessen breakage and improve speed
- Remarkable tensile strength, lower chance of breaking or getting torn under tremendous pulling force and heavy load condition. Stable structure, great erection, less likely to snap. Minimal expansion and contraction rate, usually less than 1%.
- Smooth surface, thick layer, able to improve paper surface and quality. Effectively eliminates felt marks, grain marks, blind hole marks, vacuum marks and so on.
|